Современным предприятиям необходимо соответствовать жестким требованиям рынка и при этом завершать проекты в кратчайшие сроки. Компании непрерывно выводят на рынок новые, всё более инновационные продукты, что заставляет конкурентов участвовать в технологической гонке для сохранения своей доли рынка. Для предприятий приборостроительной отрасли это особенно актуально. Здесь одной из составляющих успеха в конкурентной борьбе является эффективное взаимодействие между разработчиками печатных плат. Но возрастающая сложность задач, «ручное» выполнение рабочих процессов и частое внесение изменений повышают риски при внедрении печатных плат в новые изделия.
Процесс разработки печатных плат требует своевременного взаимодействия между различными проектными отделами и передачи корректных данных в производство. Разобщенность проектных данных приводит к задержкам на стадии производства или, что еще хуже, к неправильному функционированию устройства, что неизбежно означает низкую эффективность продукта.
Существует множество причины проблем, связанных с расходами и задержками. Компанией Aberdeen Group было проведено исследование [1], в котором приняли участие 187 предприятий-разработчиков печатных плат. Каждое предприятие указывало свои основные проблемы управления данными о печатных платах (рис. 1).
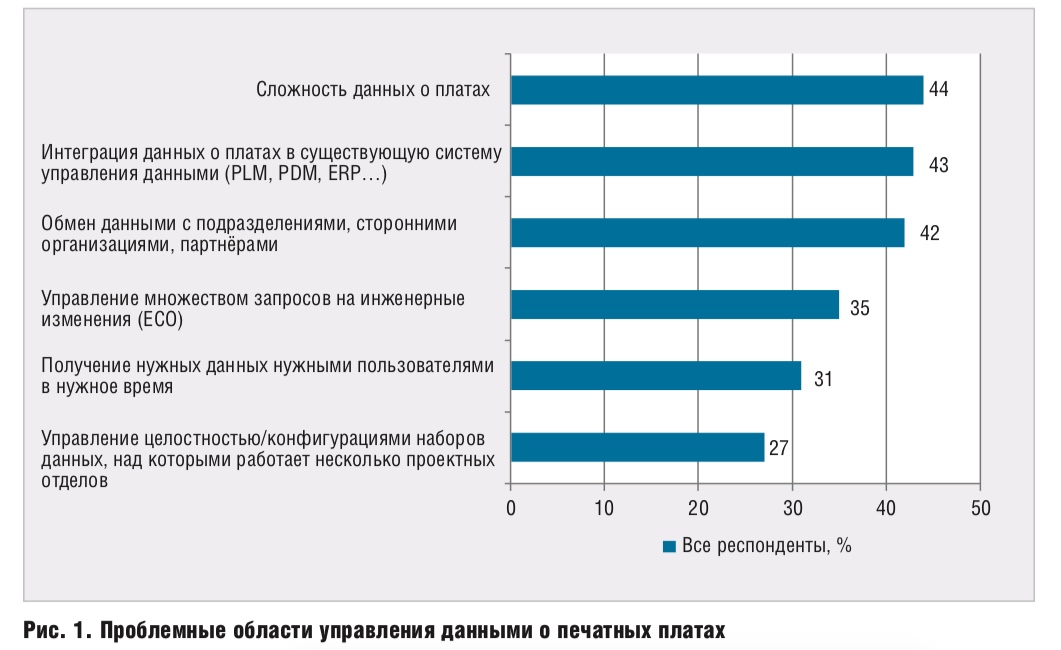
Исследователи разделили предприятия, участвовавшие в опросе, на две группы: «Лучшие в своем классе» и «Все остальные». Критериев разделения было несколько: достижение планируемой стоимости и качества готового изделия, своевременность выполнения проектов и др. Исследование показало, что лучшие в своем классе чаще конкурентов используют единый источник данных, синхронизацию проекта схемы/платы с составом изделия (Bill of Materials – BOM), доступ к данным на основе роли пользователя и т.д. (таблица 1).
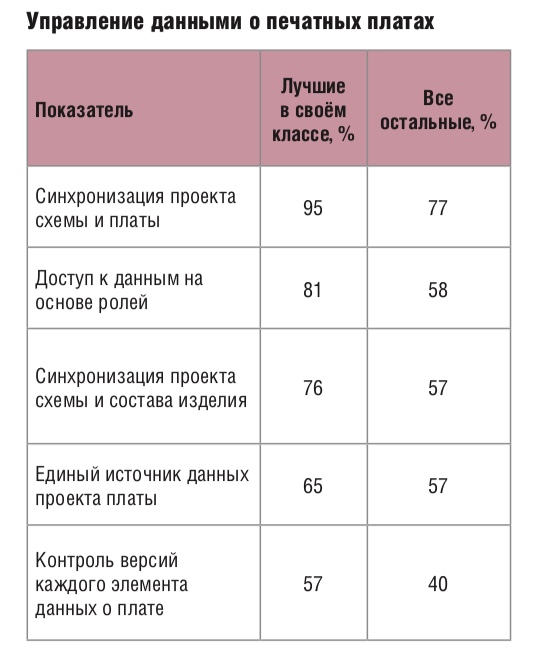
Чтобы успешно управлять данными о платах, предприятия внедряют различные решения: системы PLM, PDM, собственные разработки и т.п. Однако исследование показывает, что предприятия, признанные лучшими в своем классе, на 50% чаще используют системы управления жизненным циклом изделия (Product Life cycle Management – PLM).
Teamcenter, наиболее широко распространенная в мире PLM-система от компании Siemens PLM Software, предоставляет функционал, который позволяет управлять различными типами данных, описывающих изделие на всех стадиях его жизненного цикла. Teamcenter является универсальной системой, поскольку она обеспечивает работу как с данными CAD/CAM/CAE, так и с данными из систем автоматизированного проектирования радиоэлектронных устройств, таких как PADS, Xpedition, Altium Designer, OrCAD, Allegro.
Продемонстрируем возможности и преимущества управления данными о печатных платах с помощью системы PLM на примере интеграции Teamcenter с PADS [2].
Команды Teamcenter встраиваются непосредственно в графический интерфейс PADS, что позволяет пользователю автоматически выполнять вход в Teamcenter, открывать, сохранять и блокировать проектные данные. Интеграция Teamcenter и PADS обеспечивает разработчикам возможность импортировать и экспортировать данные библиотеки компонентов, управлять этими данными, а также получать доступ к данным о плате, управлять ими и создавать архивы данных в едином защищенном источнике.
На уровне предприятия интеграция позволяет распределенным группам разработчиков печатных плат управлять проектными данными, вносить изменения на протяжении всего жизненного цикла изделия и, как следствие, уменьшить количество повторных исправлений.
На уровне пользователя интеграция с Teamcenter поддерживает возможность открывать и сохранять «родные» проектные документы PADS, получать доступ к проверенным компонентам, управлять покупными изделиями, взаимодействовать с проектировщиками механической части изделия, создавать файлы визуального представления, передавать данные по изготовлению и сборке подрядчикам, а также создавать составы изделий, содержащие как механические, так и электронные компоненты.
Когда процессы управления проектами ECAD и библиотекой компонентов переходят под контроль Teamcenter, их можно интегрировать в процессы электронного согласования документов и управления изменениями. Благодаря управлению данными о компонентах (рис. 2) разработчики печатных плат могут сократить количество дубликатов, избежать использования устаревших или неутвержденных деталей и осуществлять закупки только у проверенных поставщиков.
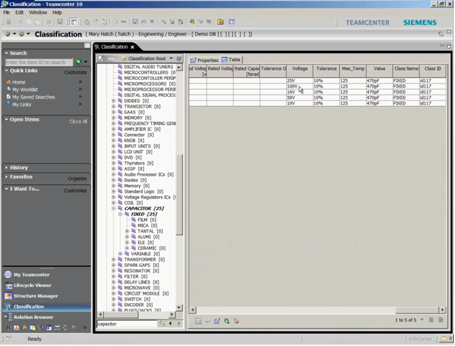
Интеграция с Teamcenter обеспечивает множеству проектировщиков работу с гарантированно точными проектными данными – благодаря использованию обменных форматов IDF и IDX (EDMD). Эти форматы позволяют передавать информацию о контуре платы, расположении компонентов и зонах запрета размещения объектов. Управляемый Teamcenter формат IDX поддерживает передачу проектных изменений, возможность принятия этих изменений или отказа от них проектировщиками механической и электронной частей изделия, а также внесения замечаний и комментариев в передаваемую информацию.
Инженеры электронной части изделия могут передавать 2,5D/3D-элементы инженерам-механикам для проведения различных типов инженерного анализа: проверки на пересечения, анализа теплопередачи, вибраций, ударных воздействий, воздействия пыли и влаги. Передача данных для проведения подобных междисциплинарных исследований позволяет повысить качество и надежность изделия.
Для быстрого выявления проблем, которые могут возникнуть на этапе изготовления, пользователи могут внедрить опциональные инструменты проверки изделия на собираемость (рис. 3) и мощные средства просмотра данных ECAD. Это позволит снизить процент брака и избежать повторных работ. Инструменты графической навигации в средствах просмотра данных ECAD позволяют проектным отделам и поставщикам просматривать и анализировать в интерактивном режиме проекты схемы и платы, вносить в них замечания.
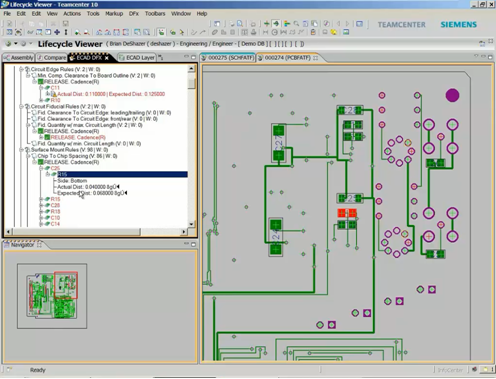
Таким образом, интеграция программных решений Teamcenter и PADS предоставляет пользователям мощные инструменты управления данными. Аппаратное и программное обеспечение печатных плат можно связать с конкретными требованиями к проекту, обеспечив возможность их отслеживания на протяжении всего жизненного цикла печатной платы.
Автор Александр Евграфов. Статья размещена в журнале "Современная Электроника" №5 2018.