Станкостроительный завод «Саста» – современное российское предприятие с полувековой историей, сохранившее лучшие традиции советского станкопрома. Основное направление деятельности – полный цикл производства металлорежущих станков: от проектирования и литья до финальной сборки. Станки «Састы» работают на предприятиях машиностроения, ОПК, нефтегазового комплекса и экспортируются в 39 стран мира. В 2020 году на заводе завершился масштабный проект построения сквозного инженерно-производственного информационного контура на базе решений АСКОН и 1С. Рассказывает Евгений Городчук, координатор проекта внедрения комплексной информационной системы (АО «Балтийская Промышленная Компания»).
В конце 2017 года «Балтийская Промышленная Компания» (БПК) стала мажоритарным акционером станкостроительного завода «Саста» в городе Сасово Рязанской области, и нам предстояло выяснить, какие ИТ-системы есть на предприятии и насколько эффективно они работают. В процессе аудита поняли, что автоматизация имеет лоскутный характер и не обеспечивает целостности и оперативности обработки данных, необходимо менять и внедренное ранее ПО, и организационные подходы к работе.
Устаревший набор систем
Безусловно, частично процессы были автоматизированы. Но, во-первых, использовавшееся ПО устарело морально и не подлежало апгрейду. Во-вторых, каждое подразделение пользовалось своим набором программ от разных разработчиков. Это негативно сказывалось на процессах: сервисном обслуживании и решении функциональных задач подразделения. В части конструкторско-технологической подготовки документации на заводе использовались Autodesk Inventor и устаревшая конфигурация 1С: PDM. Для управления производством – самописная программа (еще на базе операционной системы DOS), которая себя исчерпала, в том смысле, что работала на пределе своих возможностей: не справлялась с обработкой накопленного объема информации, возникали проблемы с поддержкой современных ОС.
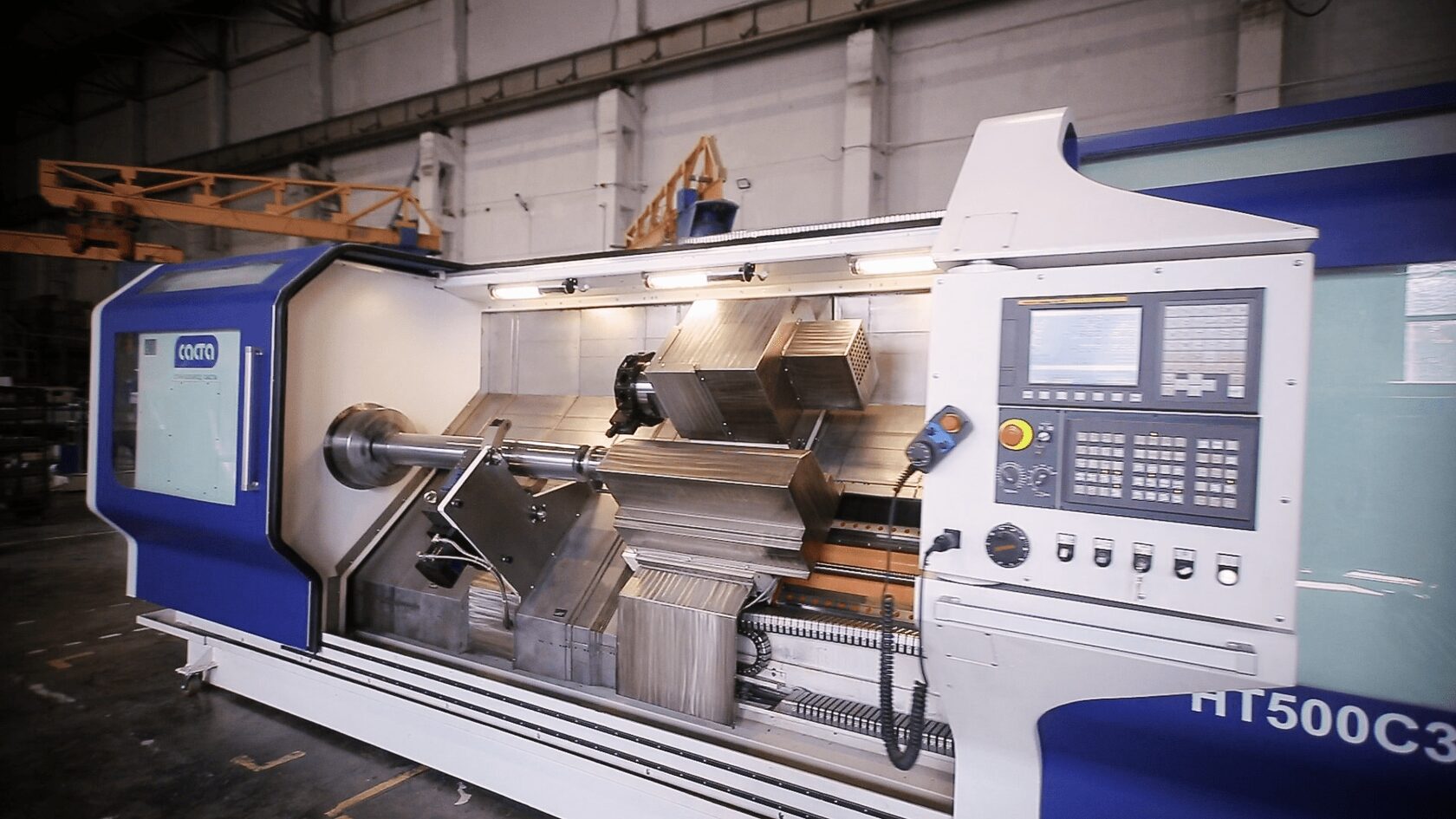
Выбор PLM-решения
Основная задача проекта автоматизации – создать единую информационную систему, которая обеспечит современную бизнес-среду для решения оперативных, учетных, управленческих задач. C 2018 года наша команда активно занималась поиском программных инструментов, параллельно решая, какие контуры нужно автоматизировать в первую очередь. На это ушло достаточно много времени.
Мы рассматривали предложения от нескольких разработчиков: АСКОН, Siemens, Топ Систем. В итоге выбрали PLM-решение АСКОН. На выбор повлияла бОльшая распространенность – по сравнению с T-FLEX PLM. Сравнивая с Siemens, конечно, мы обращали внимание на цену. Плюс в России свои стандарты проектирования, и зарубежные системы требуют дополнительной кастомизации, а мы ставили задачу максимально сохранить типовое ядро ПО. Кроме того, повлияла территориальная близость: и головной офис БПК, и офис АСКОН находятся в Петербурге, а проект внедрения сопровождали специалисты АСКОН-Рязань.
Перевод архива КД в цифровой вид и его верификация
В основе проекта лежал анализ бизнес-процессов подготовки и планирования производства. Были описаны схемы «как есть» и разработаны проекты схем «как должно быть». На основе этой информации мы совместно с командой АСКОН-Рязань настраивали систему и разрабатывали методики по работе в ней.
Начали с конструкторского отдела, потом подключили технологов. И здесь нам предстояло решить непростую задачу наследования ранее разработанной конструкторско-технологической документации: перевести архивные документы, как бумажные, так и электронные, в новую систему. Пошли по пути разработки конвертеров из используемых систем. Организовали автоматическую замену справочных покупных и стандартных изделий, элементов технологических процессов (оборудование, операции и других) на элементы справочника ПОЛИНОМ:MDM. Выполнили проверку полноты и актуальности данных по основным изделиям. Мы отказались от множества конструкторских справочников в пользу единого источника информации – ПОЛИНОМ:MDM. Таким образом была решена проблема несовпадения наименований.
Когда не справлялись конвертеры, мы переносили информацию вручную. Параллельно сотрудники исправляли ошибки, которые встречались в старой документации. Таким образом, переход на новую систему инициировал упорядочивание архива конструкторской документации, который ранее был бумажным, не полным. Мы до сих пор обращаемся к этим архивам и восстанавливаем их в цифровом виде, так как объемы информации большие и требуют много времени на проверку и перевод в электронный вид.
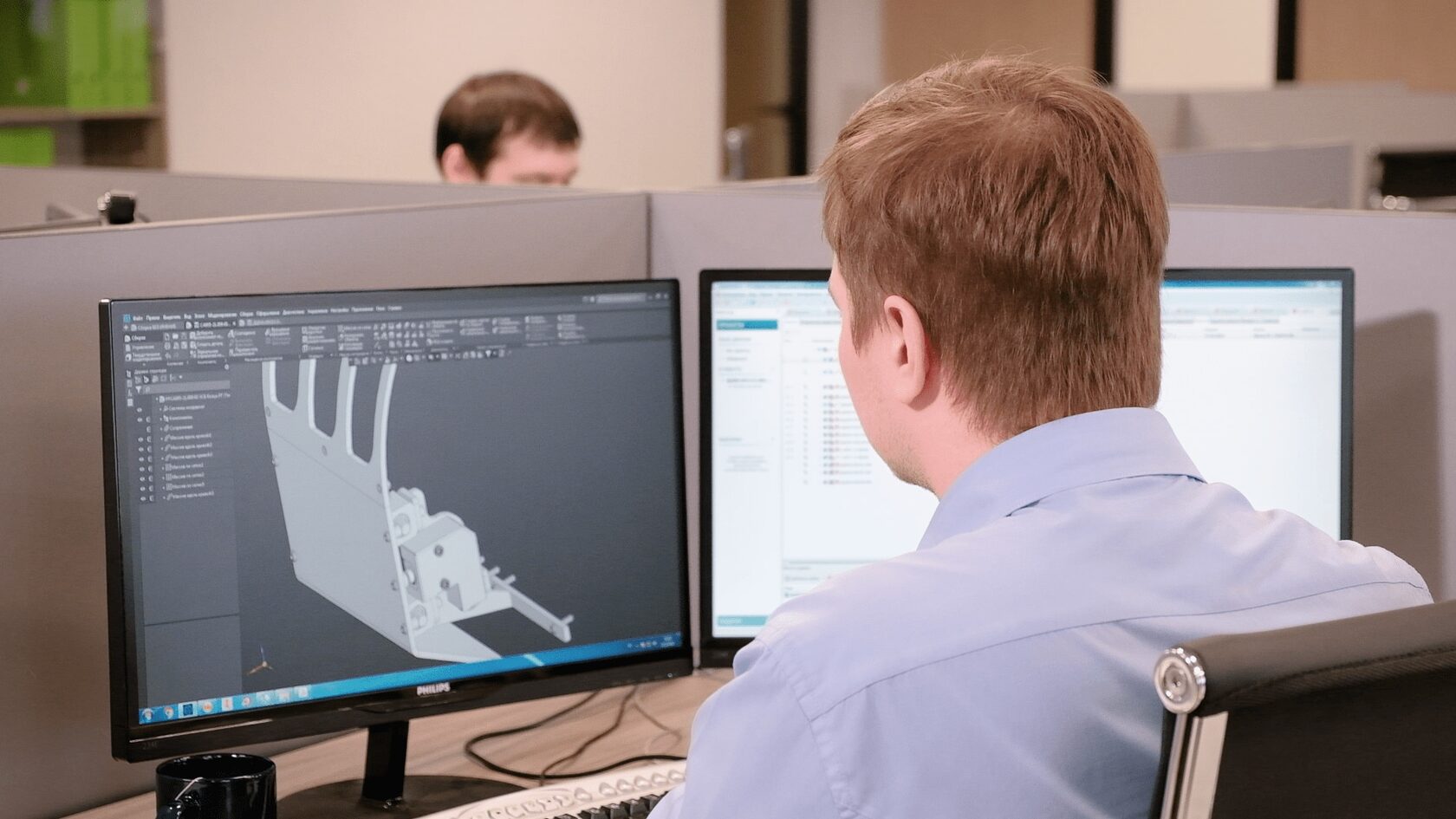
Привыкнуть к новым правилам, или работа с возражениями
Откровенно говоря, проблем было много. У каждого ПО есть свои особенности, как по интерфейсу, так и по функциональности. Сотрудники получили новые инструменты, которые работают иначе, и более жесткую систему: взамен прежних «вольностей» – единый стандарт разработки, хранения и передачи документации. Первые полгода люди привыкали, вместе со специалистами АСКОН проводили работу над ошибками. В конце прошлого года был введен административный запрет на загрузку рабочей документации из неактуальных систем.
Результаты и эффекты
Внедрение стартовало в апреле 2019 года. Первая и самая главная часть проекта завершилась летом 2020 года. К этому времени мы установили КОМПАС-3D, ЛОЦМАН: PLM, ВЕРТИКАЛЬ и ПОЛИНОМ:MDM, обучили сотрудников. Сегодня на предприятии построен сквозной инженерно-производственный информационный контур. Конструкторы работают в 3D, все согласования проходят в электронном виде. Применяются инструменты коллективной работы, когда можно оперативно прикинуть, что элементы, подготовленные разными конструкторами, корректно стыкуются друг с другом. И это, конечно, экономит время. Также в «цифру» переведено взаимодействие конструкторов с технологическим отделом: технологи получают КД и проверяют, нет ли там каких-то нереализуемых вещей, разрабатывают техпроцессы в системе ВЕРТИКАЛЬ. После этого документации присваивается статус «Активная» и она отправляется на производство. Модуль «Интеграционная шина предприятия» позволяет выгружать конструкторско-технологических данные и изменения из ЛОЦМАН:PLM в 1C: ERP. Корректность и отсутствие дублей в информации обеспечивается за счет одного ее источника — системы ЛОЦМАН:PLM.
Вся разработка документации ведется в цифровом виде. Когда разработка закончена, конструкторы отправляют документы в архив в ЛОЦМАН:PLM. Также в качестве резерва готовая КД отправляется и в бумажный архив.
Выстроенная система помогает и распределенной работе: в Сасово находится основной состав конструкторского отдела, но периодически к задачам привлекаются сотрудники БПК из Петербурга. Конструктор может удаленно подключиться к компьютеру, который находится в Сасово, либо со своего компьютера к сетевым ресурсам с помощью VPN.
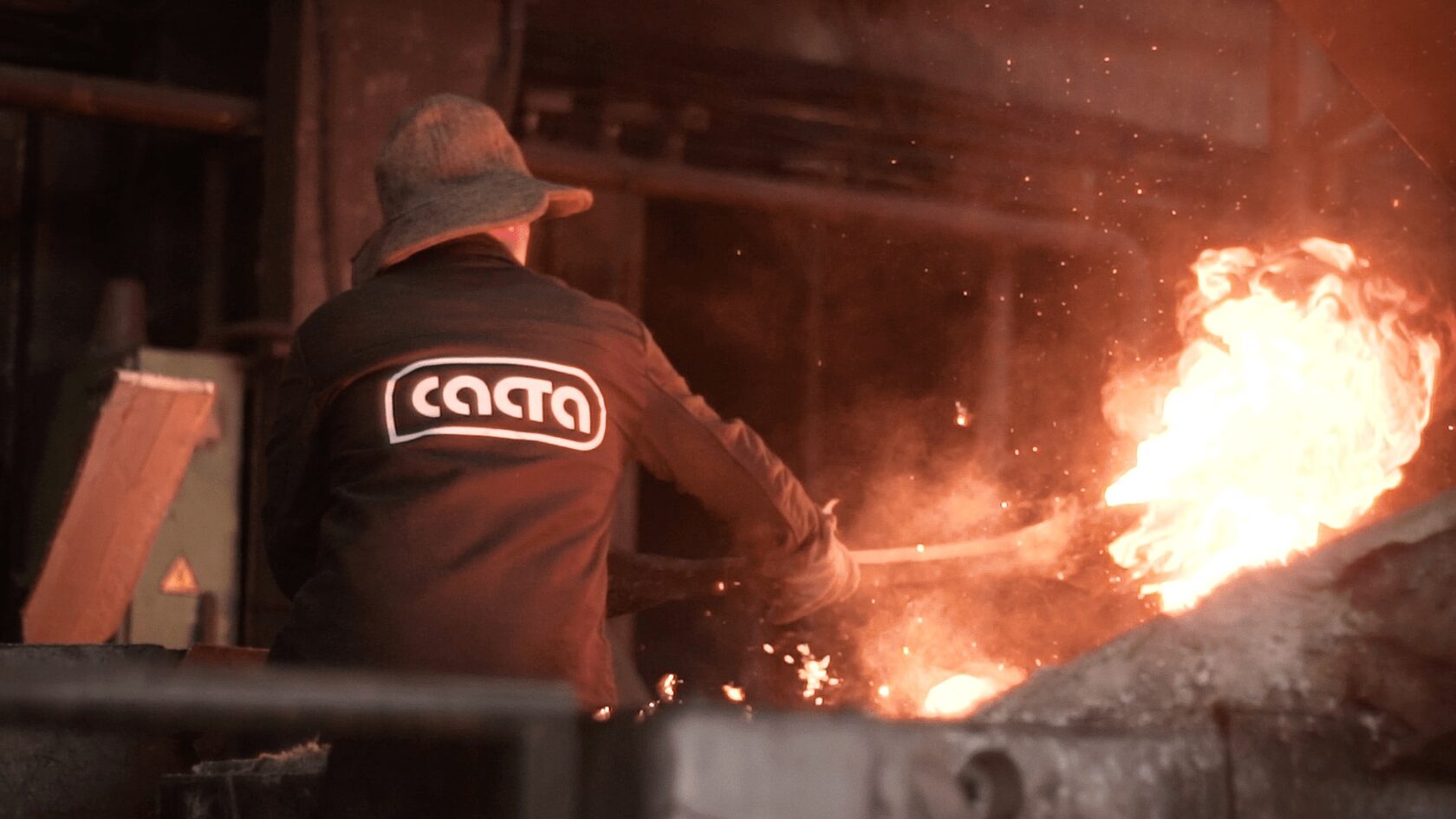
Дальнейшие шаги
Сейчас мы идем вглубь: по мере знакомства сотрудников с функциональностью ПО формулируются новые пожелания, дополнительные вопросы, которые надо решать, появляется необходимость в увеличении количества лицензий.
В ближайших планах дальнейшая доработка ЛОЦМАНа под наши бизнес-процессы, потому как ЛОЦМАН — это большой, серьезный «комбайн» с множеством функций, и понимание, как функционируют его отдельные части, приходит в процессе эксплуатации, когда набираешься опыта.
Также хотим запустить тестирование веб-клиента ЛОЦМАН. Чтобы производство и технический контроль могли просматривать эталонные чертежи через браузер, без установки полноформатной версии ЛОЦМАН:PLM.
Из задач более отдаленных — двигаться в направлении полностью безбумажного документооборота, отказаться от бумаги на производстве. Конечно, это требует больших вложений, прежде всего, финансовых.
Необходимо максимально автоматизировать обмен данными между ЛОЦМАН:PLM и 1С, — до сих пор это является узким местом, информацию выгружает специально выделенный сотрудник.
Планируем продолжить осваивать решения, которые предлагает АСКОН. Расширить автоматизацию в части конструкторских расчетов — с помощью расчетных приложений для КОМПАС-3D. Еще более активно использовать возможности ПО для совместной разработки, чтобы распараллеливать разработку КД между бóльшим количеством конструкторов.